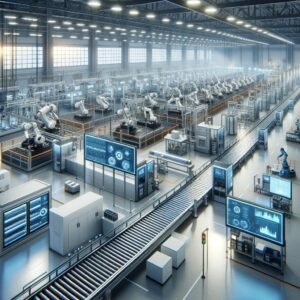
Simulation Driven Design
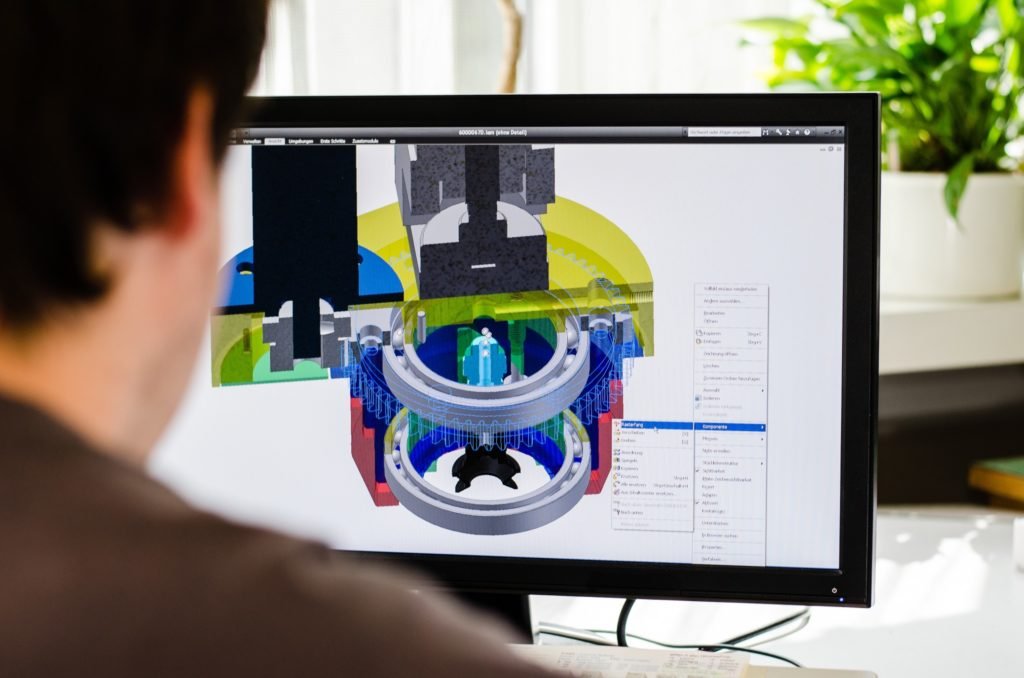
In the field of engineering, time is one of the most valuable resources. Every hour spent on design, prototyping, and testing directly impacts project budgets, creating the need for more efficient ways to work. This is where engineering simulation becomes an essential tool, allowing engineers to evaluate, optimize, and validate designs before moving to production. In this blog, we will explore how simulation can drive the design process, reducing work hours while improving the precision and quality of products.
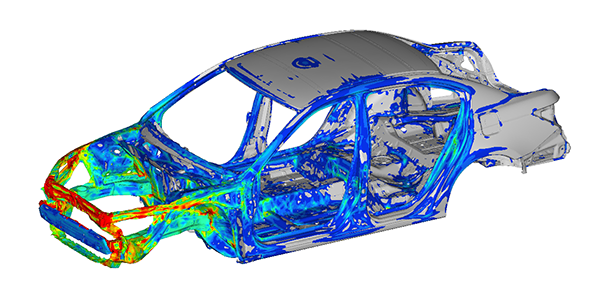
1. Eliminating Costly Physical Iterations
Traditionally, designs went through numerous iterations of physical prototypes to verify functionality, performance, and durability. While effective, this process is extremely costly and time-consuming. With simulation, engineers can create virtual models of their designs and subject them to rigorous tests in controlled environments before building a real prototype. This means that many design issues can be identified and solved early on, eliminating the need for multiple physical prototypes.
2. Better Data-Driven Decision Making
Simulation provides a wealth of data on how a design performs in different scenarios. Engineers can simulate extreme conditions, test different materials and design variations, and observe how each modification affects overall performance. This data-driven approach allows for more informed and accurate decision-making, which not only improves the final design but also reduces the time spent on testing and validation.
3. Optimizing Design from the Start
One of the biggest benefits of simulation is that it allows engineers to optimize the design from the early stages of the project. With advanced simulation tools, potential design failures can be identified and corrected, efficiency can be improved, and material or cost reductions can be achieved without compromising quality. This means that final designs tend to be more refined and efficient, reducing the need for later revisions and speeding up the time to market.
4. Reducing Human Errors
Manual design is subject to human errors, which can be costly and time-consuming to fix once the manufacturing process has begun. Simulation automates much of the analysis process, eliminating the possibility of calculation mistakes or incorrect assumptions. Simulations can also be run multiple times without adding cost or time, increasing confidence in the results before moving on to production.
5. Simulating Extreme Conditions
In many cases, it is difficult or unfeasible to recreate extreme conditions in physical tests, such as high temperatures, intense vibrations, or extreme loads. With simulation, engineers can subject their designs to these conditions virtually, allowing them to understand how the product will behave in real-world situations without the risk of costly physical failures. This is especially useful in industries like aerospace, automotive, or energy, where safety and performance under stress are critical.
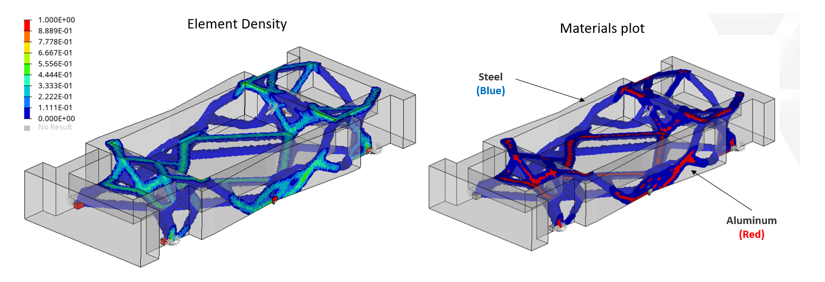
6. Multidisciplinary Simulation
Engineering simulation not only allows modeling of one aspect of a design but also facilitates the analysis of different disciplines simultaneously. This includes thermal, structural, fluid dynamics, and electromagnetic simulations, among others. By combining multiple analyses within a single simulation, engineers can see how different parts of a system interact and resolve potential problems that might go unnoticed in independent tests. The ability to evaluate the design from various perspectives reduces the need for multiple simulations, thus decreasing the hours spent on the process.
7. Development of Virtual Prototypes
The use of virtual prototypes, also known as digital twins, has revolutionized the way companies develop products. A digital twin is a virtual replica of a physical system that allows for testing design, manufacturing, and operations in a digital environment. Engineers can use these models to optimize the entire product lifecycle, from design to maintenance and continuous improvement. The ability to test virtually before manufacturing saves a tremendous amount of time in design and development.
8. Improved Collaboration and Communication
Modern simulation tools facilitate collaboration between engineering, design, and manufacturing teams. With shared virtual models, teams can work together in real-time to identify problems and make adjustments. This reduces the need for face-to-face meetings and long discussions, allowing multidisciplinary teams to work more efficiently and without friction. In turn, this shortens feedback loops and improves the quality of the final design.
9. Reducing Time to Market
One of the biggest advantages of using simulation in design is the significant reduction in time to market. By identifying and solving problems faster, companies can bring products to market more quickly, giving them a competitive edge. In addition, the savings from physical prototypes and fewer iterations allow more resources to be allocated to other areas of product development or to improve production capacity.
10. Real-Time Simulation and Continuous Optimization
The evolution of simulation technologies has reached a point where real-time simulations are now a possibility. This means that engineers can test a design in real-time while developing it, making dynamic adjustments based on the results obtained. This capability allows for continuous optimization of the design and on-the-fly changes without restarting the process. Continuous optimization based on real-time simulations not only saves time but also results in higher-quality final products.
Example: This is a topology optimization by Hyperworks Optistruct
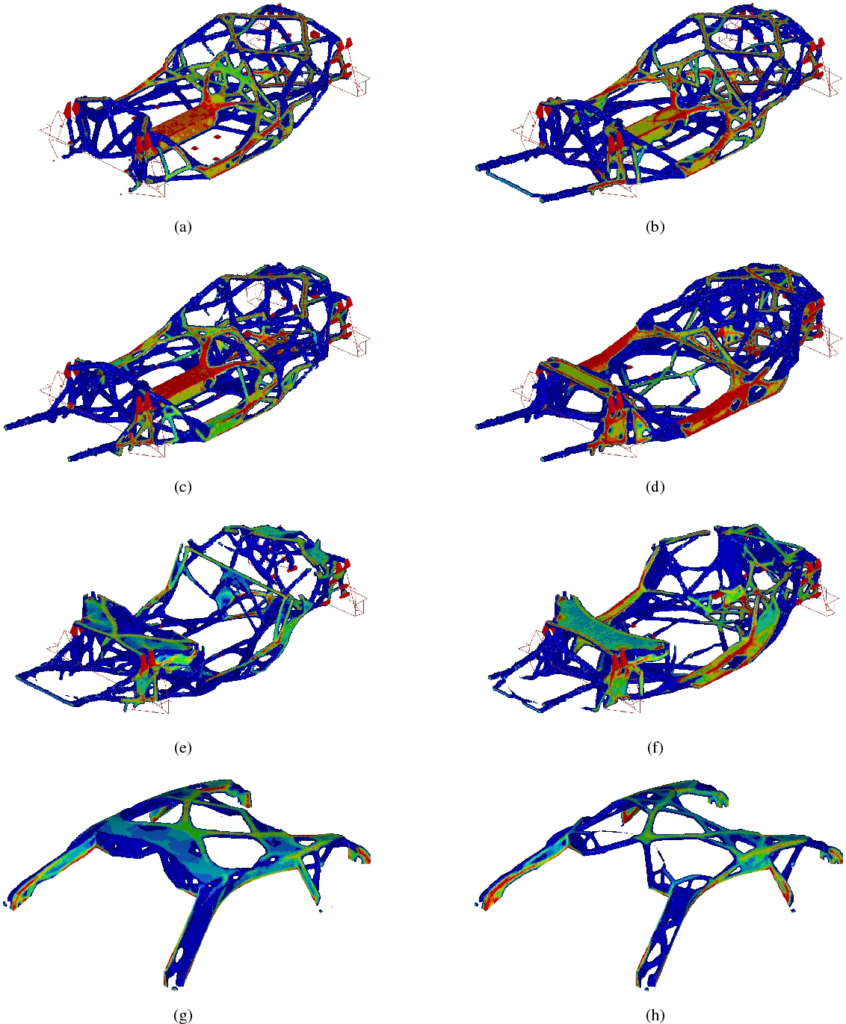
ymer@hyemtech.com
Leave a Replay
Conclusion
Engineering simulation is a powerful tool transforming the design process, allowing engineers to save hours of work while improving product quality. By eliminating physical iterations, optimizing designs from the outset, and facilitating collaboration between teams, simulation not only reduces development costs but also speeds up time to market. For companies looking to stay competitive in an increasingly fast-paced world, adopting advanced simulation tools is not just an option—it’s a necessity..
Recent Posts
Follow Us
Weekly Tutorial
Sign up for our Newsletter
Click edit button to change this text. Lorem ipsum dolor sit amet, consectetur adipiscing elit